(WXYZ) — If you are planning to do any construction at your home, prepare for sticker shock.
The National Home Builders Association says increasing prices could cause the price of an average new single family home to increase by more than $18,600.

Source: TradingEconomics.com
Last May, lumber prices hit record highs, and then timber! They fell. Now: bad news for do-it-yourselfers and builders — they are building back up.
At Hines Drive and Ann Arbor Trail, Infinity Homes Founder Rino Soave is building the Park Row apartments in Westland. This is how he describes lumber prices since the pandemic started: "It was like a rollercoaster."
And when you look at the data, you can see why.
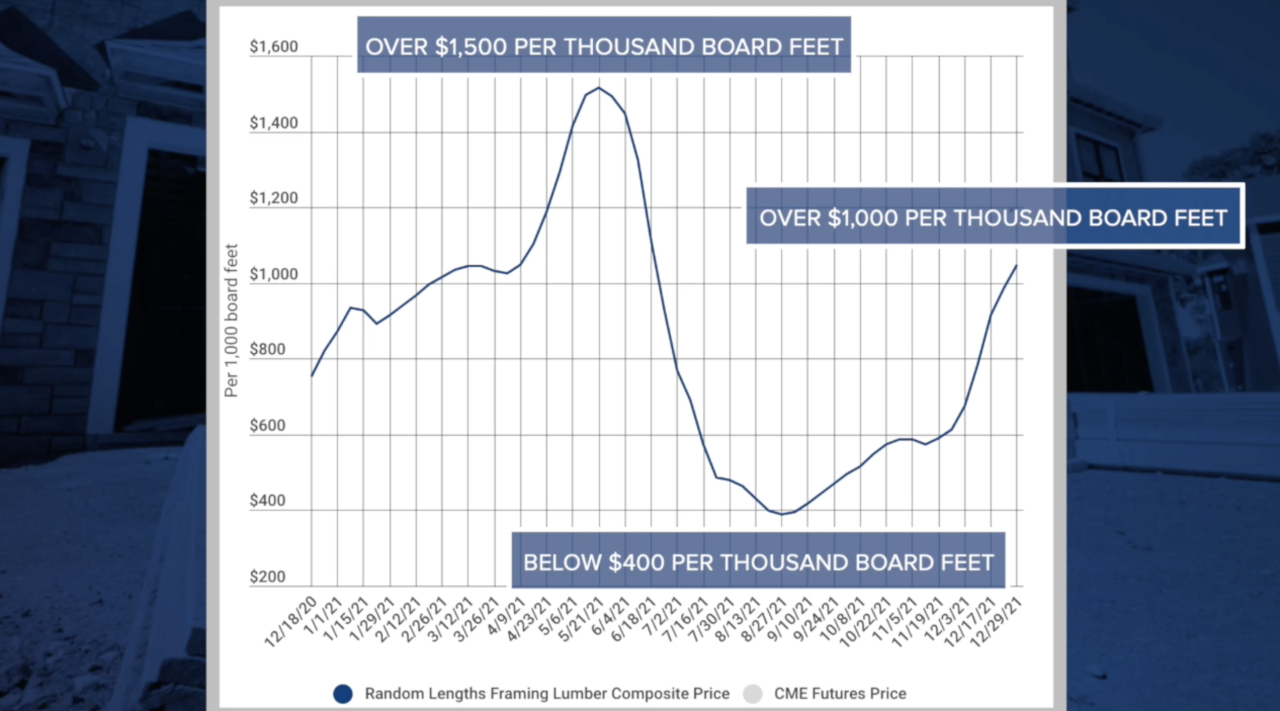
According to Random Lengths Lumber, prices hit more than $1,500 per thousand board feet in May. It then dropped in August to below $400.
And now, once again is up big time, costing more than $1,000 per thousand board feet. It is driving up the cost of building homes.
"It is a shame because our company prides itself on, and I think we are one of the few players in the industry, that caters to that step up market," said Soave. "Now that same house you could have bought maybe 18 months ago for 220 is now probably close to 280. So it is a big spike. And the fear is the attainability of housing is going to be out of reach for some people."

Sheldon Yellen is CEO of Belfor. The international disaster response company is based in Livonia.
"Pricing, if you go back a couple years ago, OSB board was $8-9 a sheet. Over the last few months it has gone as high as $50 to $55 a sheet," said Yellen.
With his eye on the global markets, we asked his thoughts on what is causing this. He says natural disasters increased demand for his services. His need for materials is up about 22 percent.
"I think there is some impact on the amount of work that is going on and required because of whether it is wild fires, hurricanes, tornadoes," said Yellen.

However, he and industry analysts blame mostly COVID-19.
"I think the supply chain issues and the COVID work stoppages in some of the manufacturing facilities and plants that are producing materials are probably more significant than the actual demand itself," he said.
Belfor is trying to minimize costs and decrease the risk of lack of supplies due to shipping delays by placing larger orders earlier.
Yellen says his advice to even do-it-yourselfers working on a project now is plan ahead so that volatile prices and supply chain issues don’t leave you in a jam.

"Don’t say, 'I will get it as I need it.' You are going to have to put your money out first. You are going to have to stock and inventory a little bit, to make sure you can secure the products you need, so that each time you get to another phase of construction, you are not forced to stop working," said Yellen.
Business leaders who buy lumber all the time say they don’t see a way to nail down what is going to happen in this environment. The certainty seems to be uncertainty.